Glazing is one of the most transformative stages in ceramics, where raw, powdered materials melt and fuse in the kiln to create a dazzling array of surfaces.
You’ve thrown the perfect pot—its shape is balanced, the walls are even, and it feels just right in your hands. Now comes glazing, the final step that can elevate your piece or, in an instant, turn it into a disappointing surprise. Understanding the mechanics of glaze chemistry helps prevent those heartbreaks, giving you more control over the outcome while still embracing the magic of the kiln.
What exactly is happening behind the scenes as we explore? Exploring glaze chemistry means understanding the science behind it which not only helps demystify the process but also opens up endless creative possibilities for potters. Let’s take a closer look at how different glaze components react in the kiln and some tips for experimenting with glaze combinations.

The Basics of Glaze Chemistry
At its core, a glaze is a glassy coating that forms when ceramic materials are heated to high temperatures. At Throw Clay LA, we fire to cone 5/6, reaching temperatures of approximately 2,167–2,192°F (1,186–1,200°C), which allows for durable, vitrified ceramics with rich glaze effects.
A glaze is composed of three primary components:
Silica (SiO₂) – The Glass Former
Silica is the essential ingredient that creates the glassy surface in a glaze. However, by itself, silica melts at extremely high temperatures (above 3,000°F), making it impractical for pottery glazes.
Fluxes – The Melting Agents
Fluxes help lower the melting point of silica, allowing it to flow and form a smooth surface. Common fluxes include feldspar, calcium carbonate, lithium, and boron.
Alumina (Al₂O₃) – The Stabilizer
Alumina helps control the viscosity of the glaze, preventing it from running off the pot during firing and ensuring an even coating.
Other ingredients, such as colorants and opacifiers, influence the glaze’s appearance, giving potters a broad spectrum of colors and textures to use while exploring glaze chemistry.
Colorants are metal oxides or stains added to glazes to produce different colors. Common examples include cobalt oxide for blue, iron oxide for brown or red, and copper carbonate for green. The final color can vary depending on the glaze composition and firing atmosphere.
Opacifiers are materials that make glazes more opaque by scattering light. They prevent glazes from being too transparent and can create solid, rich colors. Common opacifiers include tin oxide and zirconium silicate.
How Glazes React in the Kiln
When a kiln reaches its target temperature, glazes undergo dramatic physical and chemical changes. Exploring glaze chemistry, here’s what happens inside:
Fusion: As heat increases, the fluxes begin to interact with silica, forming a molten, glass-like layer over the pottery.
Crystallization: Some glazes develop crystals as they cool, creating unique surface textures like celadon or satin mattes.
Volatilization: Certain materials, such as copper or barium, can off-gas during firing, influencing surrounding glazes and creating unexpected effects.
Oxidation vs. Reduction: The kiln’s atmosphere plays a crucial role. Oxidation firings (with ample oxygen) produce bright, predictable colors, while reduction firings (with limited oxygen) alter the way metal oxides develop, often resulting in richer, more varied tones.
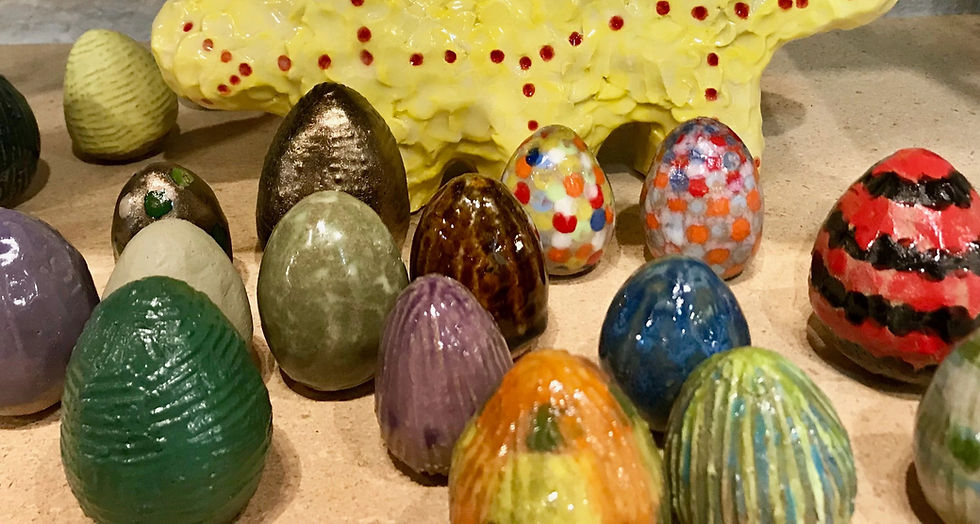
Tips for Experimenting with Glaze Combinations
Playing with glaze combinations is both an art and a science. In our Introductory Courses we keep things simple and stick to a single layer of food-safe glazes. Once you are comfortable working in the studio, and ready to start exploring glaze chemistry, here are some tips to help you explore glazes and refine your results:
Layering Glazes: Apply one glaze over another to create depth and interaction. Some glazes pool and break in interesting ways when layered.
Varying Thickness: Thicker applications may yield more intense colors, while thinner layers can produce translucent effects.
Testing Small Batches: Always test new combinations on small test tiles before committing to a large piece.
Adjusting Firing Temperatures: Some glazes shift dramatically at different temperatures—speak with studio staff before attempting to experiment with temperatures.
Documenting Results: Keep detailed notes on your glaze recipes, firing schedules, and application techniques to replicate successful outcomes. Don't get lost when exploring glaze chemistry! You would hate to find an amazing combination that you forgot to document.

Embracing the Magic of Glaze Chemistry
Glaze chemistry blends science and creativity, offering potters the opportunity to fine-tune their finishes while embracing the unpredictable beauty of kiln alchemy. Exploring glaze chemistry allows you to understand the interactions between materials and test new combinations, you can develop a signature glaze style that reflects your artistic vision. So, grab your test tiles, mix up some experiments, and let the magic of glazes inspire your next masterpiece!
The science behind glazes is truly fascinating—there's so much more to it than simply mixing colors! I’ve always been intrigued by how different compounds can affect the final outcome, and the chemistry behind it is like magic. It’s also important to remember that the quality of materials plays a crucial role in achieving the desired results. For those looking to get the best materials for their ceramic work, working with reputable chemical suppliers is key. At Brody Chemical, they offer high-quality, specialty chemicals that can help create more consistent and vibrant glazes, making it easier for artists to perfect their craft.